Case Studies: Results From Recent Clients
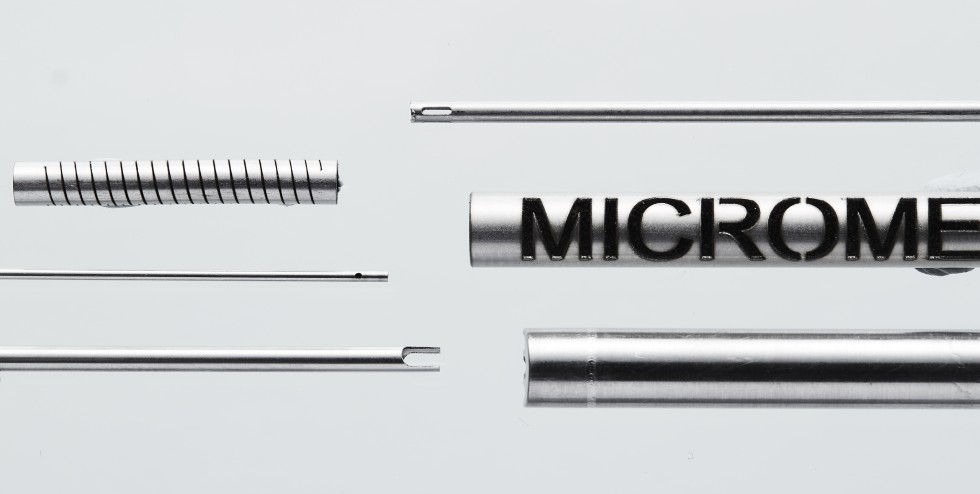
Here's the latest results from some of our recent clients. If you have an enquiry about one of our services, contact us here.
Cosworth Ltd.
When Cosworth Ltd, a top tier UK based engine manufacturer, approached us with an idea for a new filter screen we knew that we would need to be creative in our approach to the project.
The screen required 0.6mm holes across a reasonably sized area, this had the potential to cause problems due to the lack of material between each hole and the difficulty of clearing debris once cut.
Cosworth worked with our team of specialists to design the product in order to run a series of trials to find a good cleaning method and discern if the hole size and gap between the holes was feasible without the material warping when being cut.
There were two steps in this process, feasibility testing and full size cutting. We started the process by running tests on differing gap sizes between holes, once we found the optimal gap, we could then run tests on the full-size product.
As you can see from the image (right) the trials were a success. This exploration has not only given us details about cleaning fine holes in aluminium and what gap between holes can be achieved. But it has also given the customer valuable information for the future and the trust in the expertise of our team.
It is because of this expertise that we are trusted and approved suppliers of Cosworth Ltd.
Formula 1 Support
At Micrometric we specialise in the production of fine parts and precision components, cutting a range of materials as thin as 0.05mm.
It was this expertise that was required when a leading UK based formula one team came to us with a job to cut thin shims. Their team even expressed that they struggled to find a company to cut the very thin tolerances required and on a tight turnaround.
The stainless steel shims (picture left) for this customer were long, reaching 600mm, and narrow at approximately 10mm. This can be tricky as the material can warp with the heat while cutting.
With Micrometric’s expertise in cutting thin material this was not a problem and our team produced the finished parts to the customer 1 week after the enquiry originally came in.
This work is an example of our commitment to the production of quality components even within a short timeframe.